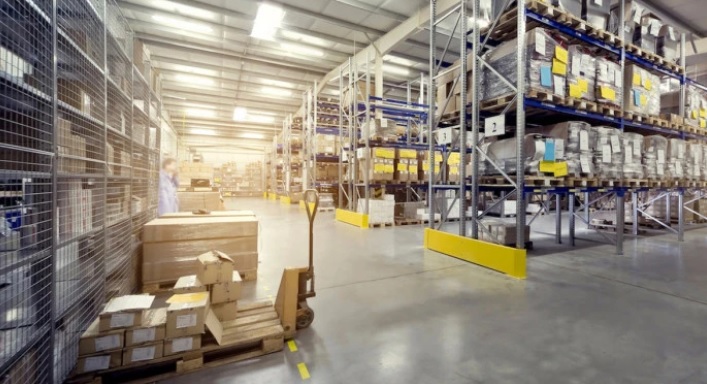
Nowadays, warehouses have gotten busier – with various rows of shelves and a rising desire for faster and better fulfillment. In recent years, warehouse technology has developed to accommodate rising complex working days. Next-generation technology such as those provided by JD Edwards Managed Services can create a more efficient and safer work environment for employees and management.
Technology has always evolved and has influenced most of our lives – and this growth is advancing, making it hard to predict in the near future.
This is particularly true in the aspect of warehouse management, logistics, and distribution. If you have visited a warehouse recently, you must have noticed the smarter ways of doing things now.
A smart warehouse can be hard to navigate, particularly if you consider the speed at which new goods are brought into the market. There are recent warehouse safety technologies coming up in the manufacturing and logistics sectors to ensure adequate workflow and guarantee the safety of employees.
But, no matter how each technology may seem, it cannot replace the necessity of proper operator training. Below is a list of the five next-gen technologies that make warehouses safer for workers.
1. Merchandise moving robots
The days of picking that are riddled with errors are way behind us. Today, warehouses can make use of almost-perfect picking rates when merchandise picking and moving elements are introduced into the system.
There are a lot of tools that can be used to encourage the picking process such as robotic order picking and order picking automated by voice. These next-gen technologies utilize bar-coding options that can be integrated easily with system management software for accurate and fast automated reporting.
Robots are becoming popular in automation. Although humans pick up items from the shelves, robots are programmed to carry more massive things through long distances in the warehouse.
Because these machines can’t think creatively like humans, they are scheduled to recognize humans along the way and other obstacles that they might encounter along the way. With these robots doing most of the heavy lifting, the warehouse becomes safer for workers because they can avoid unnecessary hazards.
2. Automatic guided vehicles
AGVs make storage and retrieval faster in your warehouse. Integrating AGVs are becoming more popular as technology improves – but even as such, the models that have already been used in the past have proven very effective and safer, and have provided a better return on investment and better protection for employees.
Some vital functions performed by AGVs include a rack, pallet, and other storage, and can automate and control the whole receiving process.
3. Eye-tracking glasses
These are mostly used to evaluate the performance of workers while they work. There are various inefficient and unsafe work practices that might occur when no one is watching. A tech provided has made an eye tracker that is wearable, designed to view the natural behavior in a work environment.
These devices can give great insight regarding the practices of workers to detect any method that is inefficient and unsafe. The eye trackers give user real-time information on what a person is looking at while they perform their regular duties.
In addition to research purposes, the devices can help managers see practices that many be unsafe for employees, including places in the warehouse that could cause an accident or a disruption.
4. Mechanical order picking
This device is attached to a pallet and transforms every slot to a storage position from a dynamic to a static one. It makes it possible for products found on a stretcher to be seen right from the aisle.
When employees are regularly reaching to pick items, they might encounter back injuries, strains, or sprains. This device can handle about 1200 pounds, thereby getting rid of the need for employees to have to stretch to reach a storage area to get products.
The pick planks can be used to carry goods in the storage area for workers to unlock guides and then place them back to the front position, therefore significantly improving the process of picking.
5. Storage and retrieval systems that are automated
These systems have been used for many years now, and although they significantly improve accuracy and throughput, they are clunky, expensive, and not very flexible. But storage and retrieval systems made nowadays are much better.
They have been of great benefit to businesses by reducing the cost of labor, increasing accuracy, and preventing work-related injuries for employees.
Leave a Reply